Переважна більшість тонкостінних деталей для саморобних авіамоделей виготовляється методом формування зі склотканини, або витяжкою з листових термопластичних пластмас. Останнім часом спектр доступних матеріалів для роботи над капотами, обтічниками коліс та подібними деталями змінився та значно розширився. Одночасно з появою полістиролу і ABC-пластика багато раніше популярних технологій стали відходити на другий план. Так, коло застосування композиційних матеріалів обмежилося лише високонавантаженими деталями (фюзеляжі кросових планерів та великих моделей літаків, корпуси гелікоптерів). У наборах, що серійно випускаються, вся формована листова «дрібничка» стала пластмасовою. Із сучасних поширених термопластів найбільш міцний ABC-пластик, який зараз нескладно купити і в деяких модельних магазинах. У нього є одна важлива перевага — він не розчиняється ацетоном. Але купити цей пластик – справа непроста. Легше дістати листовий полістирол завтовшки 1-1,5 мм. Він, хоч і не такий міцний, як ABC-пластик, здебільшого задовольняє всім вимогам моделістів. Відразу зазначимо, що наявний у продажу листовий полістирол має набагато більшу в'язкість і знижену крихкість у порівнянні зі звичними побутовими полістиролами, а також що він чудово клеїться ціакринами. Зазвичай застосовується полістирол білого кольору. Для копій краще пошукати сріблястий. Пофарбовані деталі із пластику такого кольору набувають дуже реалістичного вигляду в міру зносу покриття. Для виготовлення прозорих деталей все ж таки найкраще підходить оргскло товщиною 1-1,5 мм. Але тут можна згадати і про прозорий полістирол, хоча його світлопроникність дещо гірша.
На фабриках та у більш-менш обладнаних майстернях для витяжки пластмас найчастіше використовується вакуумний метод. Нині всі вакуумні насоси, які можна було приватизувати вже приватизували, а те, що можна купити, коштує дорого. Тому розглянемо саму що не є «домашню» технологію. Як оснащення, в першу чергу, необхідна болванка (пуансон). Виготовляють її з липи, бальзи чи щільного пінопласту. Бальзову болванку необхідно загрунтувати для зміцнення поверхні. Підходящий склад грунтовки можна приготувати, додавши в нітролак тальк (або дитячу присипку, яку купують в аптеці). При збільшенні вмісту тальку утворюється шпаклівка, за допомогою якої легко виправити дефекти поверхні. Якщо використовується щільний пінопласт, необхідно покрити болванку паркетним лаком або епоксидною смолою, розведеною ацетоном. Робочі поверхні болванки слід натерти стеарином (свічкою) або поліроллю, почекати близько години і трохи розтерти вовняною тканиною. При цьому пластмаса, що штампується, буде легше ковзати по поверхні пуансону і одночасно зменшиться місцеве потоншення матеріалу. Існує кілька способів витяжки, кожен з яких вимагає свого додаткового оснащення.
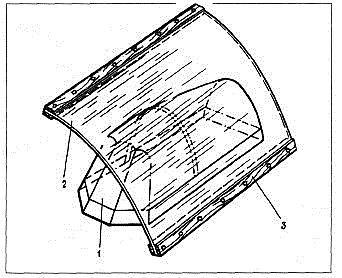
Перший спосіб
Застосовується для неглибокої витяжки дрібних деталей. (Тут і надалі передбачається, що вироби мають лише позитивну кривизну по всій поверхні). Лист термопластика з двох протилежних країв обжимається смужками фанери завтовшки 4-10 мм із застосуванням гвинтів. Двома плоскогубцями лист утримується над електричною плиткою, розігрівається до пластичного стану, а потім їм вручну обтягується вся болванка або її частина. Замість плоскогубців можна використовувати струбцини, або у фанерних окантовках зробити спеціальні ручки, що дозволить докласти більшого зусилля. Бажано, щоб при роботі температура повітря в приміщенні була не нижче 20 ° С, - при нижчій температурі пластмаса швидко остигає і втрачає пластичність. Якщо після дотику до болванки матеріал встигає затвердіти ще до закінчення процесу витяжки, пуансон можна підігріти в духовці до 50-6СС (це не відноситься до пінопластових болванок). До недоліків методу відноситься те, що при нагріванні лист звужується посередині, а краї його підвертаються. Це змушує викроювати заготівлю з великими припусками.
Другий спосіб
З фанери завтовшки 4-10 мм виготовляють рамку з таким розрахунком, щоб через неї проходив пуансон із зазором на бік, рівним 1,2-1,5 товщини пластику. Робочі кромки рамки мають бути закруглені та ретельно зашліфовані. До рамки прибивають бруски, які будуть її підставою. Ширину заготовки з пластмаси беруть утричі більше за розмір отвору в матриці. Пластик нагрівають до повного розм'якшення (при цьому він сідає), накладають на рамку, і руками або струбциною пуансон продавлюють в отвір матриці. Не відпускаючи пуансон, пластмасі дають охолонути, після чого знімають із болванки готову деталь. Загальна перевага цього способу - мінімальне витончення матеріалу. Іноді у виробі утворюються складки. Це залежить від форми деталі, а може бути викликане надмірним зазором між матрицею і пуансоном, або недостатнім нагріванням пластмаси.
Третій спосіб
У цьому випадку виготовляються дві ідентичні рамки-матриці. Штампований матеріал затискається між ними, як при першому способі. Якщо нагрівання матриць із пластиком буде проводитись у духовці, то рамки можуть бути абсолютно однаковими. Температуру слід підбирати дослідним шляхом, починаючи з 70°.
Іноді, особливо при невеликих розмірах деталі, зручніше нагрівати пластик над електричною плиткою. Це дозволить спостерігати за зміною стану матеріалу. У такому разі одна з рамок (калібруюча) повинна мати зазор 1,2-1,5 товщини матеріалу за контуром болванки, а друга - близько 7 мм (матрицю потрібно тримати над плиткою вниз рамкою з великим зазором). Коли пластик почне провисати, він готовий до витяжки. Сильне випаровування матеріалу з поверхні – ознака перегріву. При установці пуансона на столі обов'язково використовуються упори, що запобігають зайвій глибині витяжки (інакше деталь може вийти витонченою). Для зниження потоншення пластмаси затягування болтів, що стягують рамки, можна зменшити, щоб матеріал міг висуватися в зону витяжки.
Четвертий спосіб
Застосовується в тому випадку, коли виріб має елементи, що виступають, або поглиблення (наприклад, ребра на капоті). Знову ж таки необхідно виготовити матрицю. Її внутрішні розміри повинні бути більшими за габарити йолоп-пуансону на товщину матеріалу. Домогтися цього обробкою за шаблонами непросто, тому можна вдатися до невеликої хитрощі. Повсту слід покрити розділовим шаром (мастика для підлоги, поліроль, стеарин), і потім розтерти до блиску. За допомогою кисті або розпилювача нанести на неї кілька шарів епоксидного розклеєного клею. Кількість шарів треба заздалегідь визначити на дослідному зразку будь-якого матеріалу, щоб їх сумарна товщина дорівнювала товщині пластику після витяжки (приблизно половина її вихідного значення). Після затвердіння клею поверхню покривають ще одним розділовим шаром, і обклеюють спочатку тонкою, а потім товстою склотканиною, утворюючи жорстку кірку. Потім отриману матрицю знімають і від болванки відокремлюють еквідистантне покриття з епоксидної смоли.
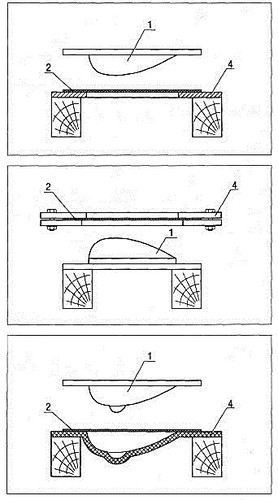
Перед формуванням пластику таку оснастку потрібно підігріти до 50-60'С (але не більше). Лист пластику розм'якшують над електроплиткою і закладають між матрицею та пуансоном, стискаючи їх струбциною або руками. Цей спосіб за своїми можливостями наближається до вакуумної витяжки. Якщо деталь має форму тіла обертання, оснастку можна виточити із алюмінієвого сплаву на токарному верстаті. На всіх представлених малюнках: 1 - пуансон, 2 - лист пластику, що штампується (витягується), 3 - фанерна рамка, 4 - плоска очко-матриця або об'ємна матриця. |